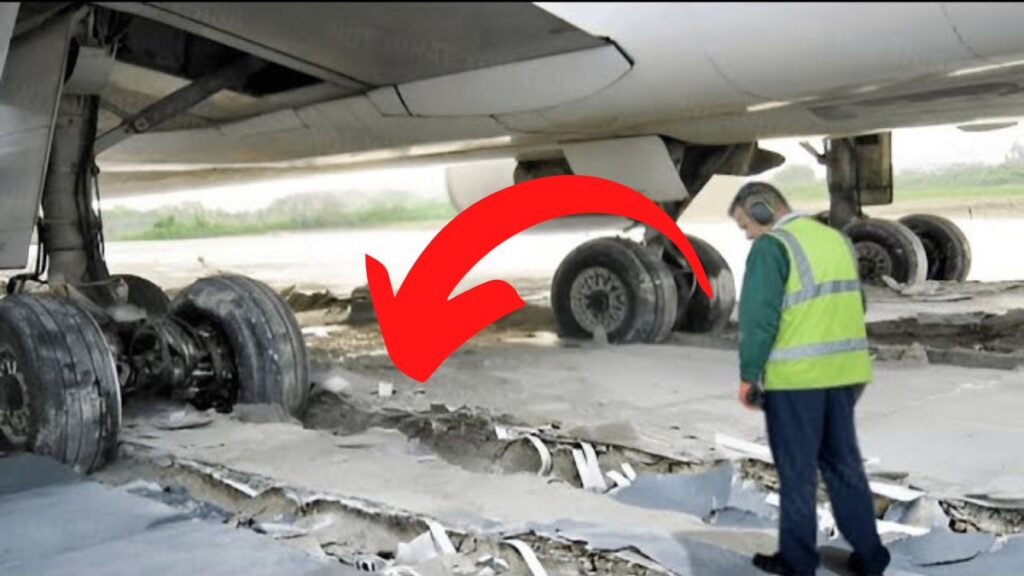
It’s not as fun as it sounds to go on a runway excursion.
It’s like going off-road, which is fun, but not so much in an airplane!
It looks like this in the best-case scenario and like this in the worst-case scenario.
Fortunately, however, there is a solution to this issue.
Some of those dangerous accidents can be avoided with the aid of this device.
It doesn’t look like a French press, but I promise you that.
And this is a unique building where the pavement actually ages quickly inside!
You may not have been aware of a number of procedures because they take place behind the scenes. Without them, our airports would see a lot more off-roading.
However, mishaps can still occur.
But what these “special” rocks actually are, what they’re made of, and how they can stop an 80-mph aircraft quickly and safely are not what you think!
A Southwest Airlines Boeing 737 overran a runway while landing at Bob Hope Airport in Burbank, California, on December 6th, 2018.
It appears that the pilot exceeded the ideal touch point.
The arrestor bed that had been installed at the end of the runway was the reason the airplane thankfully stopped.
On that, more later.
However, in addition to human error, adverse weather conditions and mechanical issues can contribute to runway excursions.
A lot of safety training is given to pilots on runways, including how to deal with emergencies, how to avoid overrunning the runway, and how to land safely in different weather conditions.
Although training is absolutely necessary, it is not always sufficient because even pilots can lose control when things get wet!
Naturally, I’m referring to hydroplaning, in which the aircraft slides on the wet runway surface with little to no control.
The water layer that forms between an airplane or vehicle’s wheels and the road or runway surface can reduce friction, making it more difficult for the vehicle or aircraft to maintain control.
The likelihood of hydroplaning is significantly increased when still water builds up on the runway’s surface.
Because of this, some runways have grooves that not only provide channels for the escape of water but also enhance the traction of aircraft tires on the runway surface.
A minimum amount of skid resistance must also be provided by the runway’s surface.
The Airfield Pavement Evaluation (APE) team is used by the US Air Force to test for this.
Additionally, the APE group has some intriguing tools: This machine measures friction and can determine the pavement’s texture depth.
The skid resistance of the runway is determined by the surface’s roughness.
Under the wheel, the nozzle releases specific amounts of water to resemble various weather conditions.
Here, on the grooved runway, the test is being repeated.
Using a hydro timer is an additional method for measuring the values of friction.
The amount of time it takes for the water to drain decreases with smoother surface.
The pavement’s texture depth can decrease over time as a result of traffic and weathering.
A skidabrader can be used to repair the pavement.
When you compare the pavement in front of the truck to the pavement behind the truck, you can see that skidabraders essentially roughen up the surface.
Despite all of these safety measures, aircraft can still overshoot the runway.
As a result, a plan B is required.
Any airplane can be brought to a quick stop once!
That’s why we said a quick and “safe” stop earlier.
Probably more like it is this!
However, why is this aircraft damaging the runway?
When it comes to preventing runway excursions, the length and width of runways are crucial factors.
The introduction of faster jet aircraft like the Boeing 707 in the 1960s necessitated longer runways.
Therefore, the FAA proposed raising the minimum runway length requirements, but the industry strongly objected.
Some airports, like LaGuardia Airport in Queens, New York, may be unable to establish this buffer zone due to their proximity to populated areas, bodies of water, and other natural barriers.
In the 1990s, the FAA began investigating new technologies that could safely bring aircraft to a safe stop in less than 1,000 feet in the event of a runway overrun in order to improve runway safety in such airports.
The Engineered Materials Arresting System, or EMAS, was the response. EMAS is a material with a high energy absorption capacity that could be installed beyond the runway ends.
EMAS is made of lightweight, crushable materials that are designed to collapse when an aircraft weighs more than 12 tonnes. It is sometimes referred to as an arrestor bed.
The aircraft slows down gradually as the landing gear rolls through the material and sinks into it.
But exactly what is EMAS, and how does it stop an aircraft traveling at 70 knots?
The EMAS is built on top of these pebbles.
Although they may appear to be rocks, their weight and ease of crushing make them more akin to styrofoam.
Most of the time, the pebbles are made of high-strength materials like expanded polypropylene or expanded polystyrene. They are made to compress and absorb the aircraft’s energy when it comes to a stop, preventing injuries and damage to the aircraft.
That was referring to an incident that took place on October 27, 2016, when a Boeing 737 carrying 37 passengers, including Mike Pence, who was running for vice president at the time, ran off the runway while landing at LaGuardia.
The airplane landed safely and without major damage thanks to the EMAS.
Prefabricated blocks are one method for installing EMAS.
Prefabricated blocks are ideal for smaller projects because they can be easily unloaded and stacked side by side.
However, for more substantial implementations, construction takes place on-site.
In order to house the pebbles, the space is first divided into sections.
After that, the pebbles are poured in and leveled.
After that, they are packed in preparation for the concrete layer that will be added as the top layer.
After the concrete has set, a coating is prepared and applied.
The top layer is shielded from the elements by doing this.
The lifespan of an EMAS installation is 20 years.
Once installed, EMAS doesn’t need much maintenance.
Patching any damages is possible as needed.
Only the damaged parts must be removed and replaced if an airplane crosses the runway and engages the EMAS.
In US airports, EMAS has been installed on more than 100 runways. As of March 2022, 18 overrunning aircraft had been safely stopped by using EMAS.
However, runway durability is just as crucial to aviation safety as anything else, which is why the pavement inside this building ages quite quickly.
These are two test vehicles that are connected to two 30-foot-long radial arms.
They are responsible for expediting pavement testing.
The vehicles can perform 50,000 cycles per 24 hours and travel at just over 31 miles per hour.
Water can also be used to create various testing environments in a controlled manner as needed.
New road designs and materials can receive expedited feedback through Accelerated Pavement Testing.
Also, are you aware of the APE team?
They look at more than just the runway’s friction measurements.
This Heavy Weight Deflectometer makes every drop look like a fully loaded C-17 flying down the runway.
The trailer-mounted apparatus works by dropping a weight that hits the pavement with up to 55,000 lb of force. The pavement deflections that result are measured to determine the stiffness of the pavement layer.
Additionally, this machine destroys runway samples by cutting deeply into the underlying materials.
After being cut out and dug up, a 6-inch core is analyzed to ensure that it satisfies the requirements.
You wouldn’t want to bury a body under a military runway for that very reason!
In order to guarantee safe and effective air travel, runway quality and safety must be ensured, which necessitates ongoing investment, maintenance, and attention to detail.
Because of this, these two are hard at work while we sleep—not those guys—these guys!